Running a tippcontainer may appear just like a straightforward method, but incorrect process can cause inefficiencies, material injury, and actually security hazards. By following correct packing techniques, corporations can save your self time, reduce fees, and ensure easy operations. This quick information outlines the best practices for launching a Tippcontainer to accomplish optimum efficiency.
Why Proper Loading Matters
Statistics indicate that incorrect loading contributes to approximately 20% of material injuries throughout transportation or handling. Furthermore, inefficient launching methods can result in more visits, ultimately causing 15%-25% larger transportation costs. For corporations running in logistics, structure, or production, these numbers may somewhat influence gain margins.

On another give, appropriate launching not just promotes detailed effectiveness but in addition reduces the likelihood of incidents, which account fully for about 30% of workplace accidents concerning tipping containers. Understanding the significance of correct loading methods may be the first faltering step to improving everyday operations.
Steps to Properly Load a Tippcontainer
1. Plan the Load Layout
Before launching a tippcontainer, generally get a few minutes to place out the way the products is likely to be placed. Deliver the weight evenly to prevent showing during transportation or unloading. Data show that uneven weight circulation triggers 40% of pot instability incidents.
Professional Hint:
Use separation barriers if you're handling multiple types of materials to prevent shifting or pairing all through transit.
2. Use the Right Equipment
Training major masses personally or with improper equipment may result in incidents and material damage. Knowledge shows that 67% of showing accidents stem from raising mishaps. Always use forklifts, hoists, or other specific gear for optimum precision.
3. Avoid Overloading
Every tippcontainer features a optimum capacity. Overloading may lead to product spillage, injury to the box, or equipment failure. Overloads are reported in 20% of jar dysfunction cases. Adhere to the manufacturer's suggested fat limit at all costs for a safer, more efficient process.
4. Secure the Load
After the products are in position, secure them effectively with straps or nets to avoid movement. This easy step may minimize the risk of sill and product damage by around 35%.
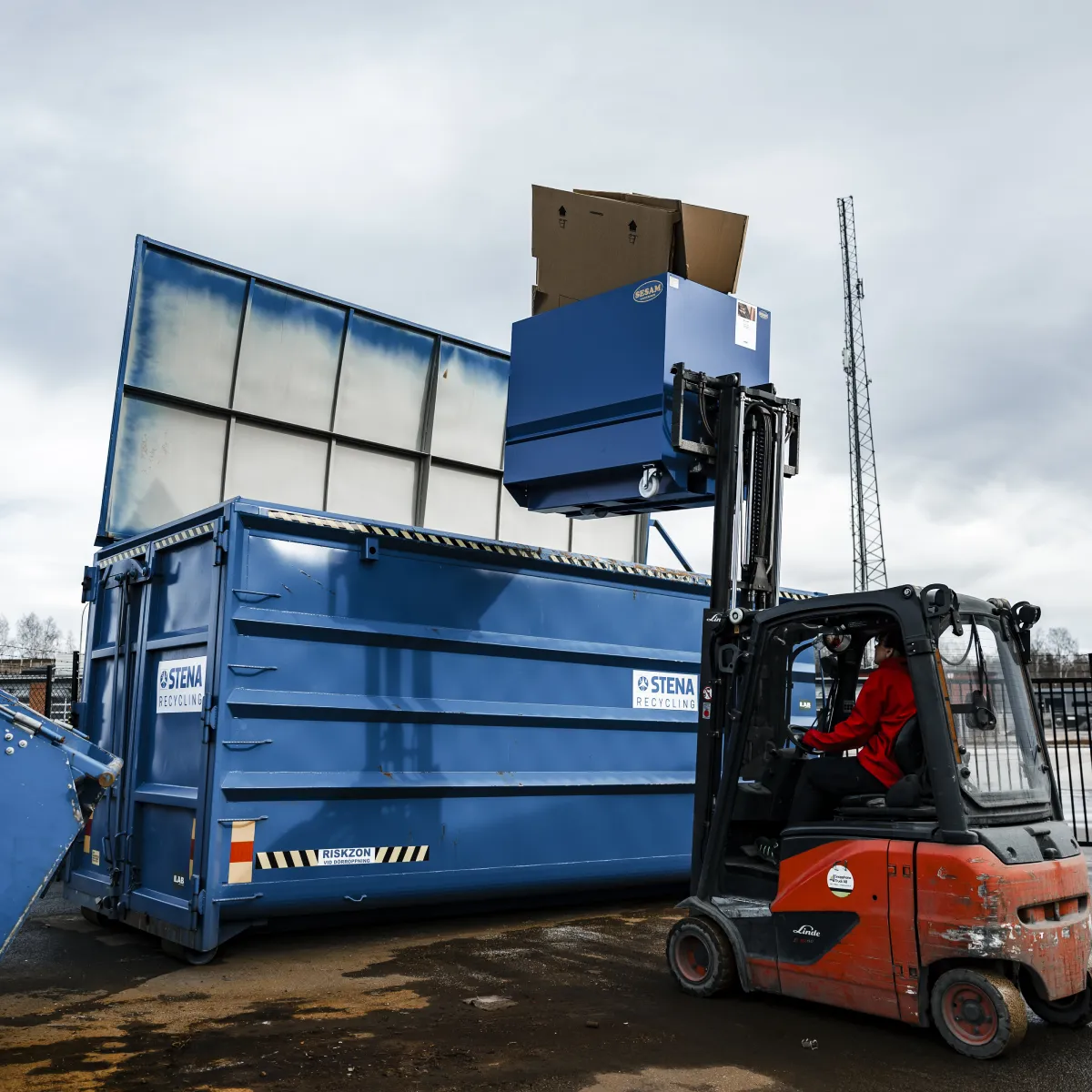
5. Perform a Final Check
Conduct a quick examination ahead of the tippcontainer is transported. Check for fat harmony, attached straps, and any signals of overloading. Reports show that a final examination reduces the risk of problems during transit by 25%.
Loading Smart, Working Smarter
Staying with these most readily useful methods might have a small additional time transparent, but the long-term benefits—such as smoother operations, less accidents, and price savings—are worth the effort. By correctly preparing, obtaining, and balancing masses, businesses can improve workflow effectiveness and minimize expenses.